Harnessing Human Intellect to Navigate AI-Driven Digital Transformation
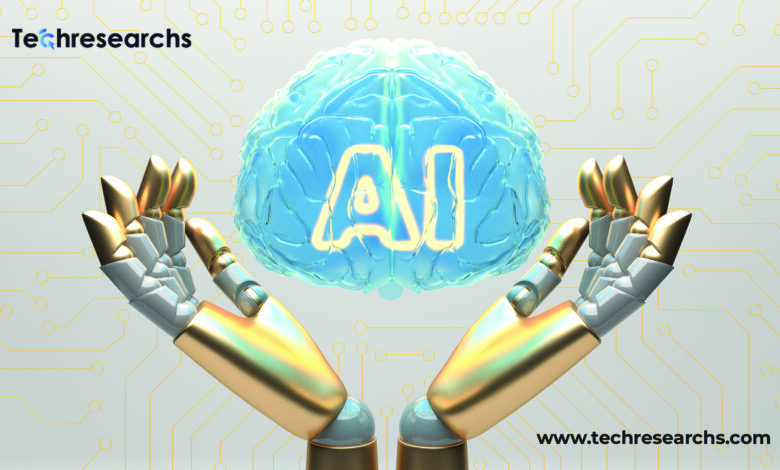
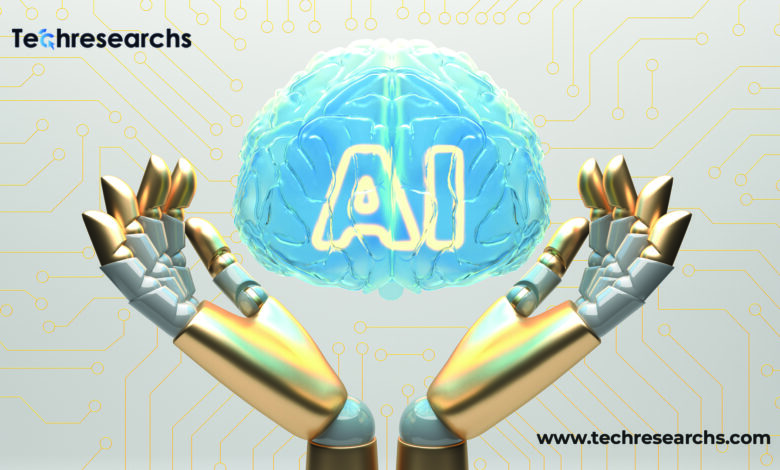
See how fostering a culture of cooperation and dialogue can help solve problems brought on by digital transformation.
Manufacturers have never-before-seen opportunities when implementing AI on the path to Fourth Industrial Revolution (4IR) ready.
Manufacturers of lighthouses are leading companies implementing 4IR technologies widely in their facilities.
By empowering industrial lighthouses with AI’s predictive and decision-making capabilities, these sectors are already profiting sustainably and achieving significant competitive, financial, and operational advantages.
For instance, predictive maintenance already enables productivity benefits for assets of up to 20%. Why are companies delaying the adoption of the Industrial Internet of Things (IIoT) when AI offers so much potential for growth in the industrial sector?
Human intellect remains the biggest determinant between success and failure, even though AI technology is driving the manufacturing revolution.
Increasingly businesses are realizing the need for employees with more sophisticated technical, cognitive, social, and emotional abilities.
As the business converts to 4IR, you’ll advance more quickly if you have higher awareness, buy-in, and collaboration from your staff.
All lighthouse manufacturers adhere to a change management strategy that values human capital at every level of the path to digital maturity.
By putting people first, many challenges to digital transformation can be overcome, including mismatched communication, a lack of support, a lack of crucial skills, and rigid organizational culture.
erroneous communication:
Many manufacturers operate in siloes with unconnected management chains and archaic communication patterns. But when dealing with difficult change-management procedures, smooth communication is essential.
Large volumes of data are shared and evaluated among many stakeholder groups in AI-driven projects. When that data is correctly acquired and organized, a comprehensive picture of operations that is visible to everyone emerges.
This business-wide view offers fresh insights that connect silos and hierarchies, according to Santhosh Shetty, a technical sales engineer who specializes in AI for manufacturing.
The teams working at the plant’s ground level are organized into compartments. They are solely accountable for one specific process and its associated tool, according to Shetty. However, the system of the plant is extremely complex and made up of numerous processes.
By enabling the business to view the plant from a single point of view, we are enabling them to emphasize the facility’s working schedules.
We can show the client where they are functioning in both high- and low-quality zones, as well as the length of time they are present there.
Because they’ve never seen the plant presented in such a comprehensive way before—across the manufacturing plant and all the interconnected processes at the same time, in one view—that is beneficial to our customers. Once everyone notices this, they all quickly agree and begin discussing what is feasible.”
Lack of buy-in:
Increasing buy-in at all levels of the organization increases the possibility that projects will receive support and accomplish their goals.
For instance, in addition to offering advice and resources, a sponsor’s involvement in a project will affect how seriously the target audience takes it.
Everyone must understand the value for the business and themselves, as well as what the journey to digital maturity will entail, from the shop floor to IT, management, and the C-suite.
People inherently oppose change, especially when it has underperformed or failed in the past, which statistically many change efforts do.
Michelin’s chief digital officer, Eric Chaniot, claimed that only 5% of the company’s success in its digital transformation is dependent on technology 2019 post at The Innovator.
Gaining the support of people you need to make the new environment successful accounts for the remaining 95% of success.
No one ever says “no,” but you can see in their eyes that they are feeling like saying it, Chaniot added.
The integrity of data is one of the most important trust-building elements in successful AI projects. Modern data science techniques give the capacity to turn raw data into what machine learning models require in order to make recommendations for optimization and offer better transparency into the AI pipeline.
Before revealing the data, detailing the assumptions and techniques the models make to Build greater trust in the resulting business insights is the responsibility of plant engineers and operators.
Lack of essential talents:
For the majority of manufacturers, the path to digital maturity is only getting started, but so is the skill pool required to create and operate digital maturity programs.
Data scientists, business intelligence analysts, machine learning engineers, and software architects are needed in multi-skilled teams for AI initiatives. These are complicated roles that call for a variety of skills to incorporate vital technologies.
The biggest obstacle to digital transformation, according to manufacturing C-suites, is a lack of skills. According to 42% of industrial businesses, there is currently a labor shortage of individuals with specific talents.
Naturally, the shift is more challenging across the manufacturing environment due to this lack.
The AI consultants you choose will have knowledge of how to handle change management problems, particularly the more systemic difficulties that arise in the early phases of digital transformation. Ask these professionals to discuss their insights on change after guiding other manufacturers along the way.
They will bring knowledge that assists strategists, project leads, and stakeholders in navigating the essential human components of change in addition to being able to assess the preparedness of a plant.
Rigid corporate culture: It can be challenging to change long-held notions that “the old way is the best way,”, particularly in the manufacturing industry. The manufacturing sector is defined by tradition, and tradition is a cultural tenet that resists easy change.
Organizational dynamics at a plant may change toward uncertainty, miscommunication, and resistance when an operational process is made more digital and data-driven.
According to Forbes, “Digital transformation doesn’t start with technology.”We observe that the organizations that excel and take the lead in transformation are those that can change their culture.
Leaders who can sway behavior and argue for increased productivity through digital transformation must imagine and implement the change they want to see.
This entails developing a culture in which people at all levels understand how to read data and take appropriate action. Members of a data-driven culture can distinguish and understand the facts, disregard bias, spot issues, and seize opportunities.
For instance, requiring executive endorsement at the highest level to ensure that company culture changes and 4IR disruptions are successful is a component of manufacturing lighthouses.
A people approach to managing manufacturing change:
Lighthouse manufacturers are aware that when risks are reduced through diligent change management, the obstacles to digital maturity dissolve. This entails giving the organization’s workforce top priority.
With integrated change and innovation, this strategy unites viewpoints and behaviors that would otherwise be incompatible. It also empowers personnel and promotes a culture of continual improvement. It is essential to first determine how much the 4IR technology is inherently enabling this transition, particularly when tying together silos and hierarchies to provide a comprehensive picture of a facility.
Currently, most manufacturers across a range of industries encounter this difficulty. You are more likely to sooner be able to exploit the complexity of IIoT if you collaborate closely with your AI partners on 4IR transformation projects.
You’ll spend less time putting out fires by bringing all of your staff along for the ride as you transition to AI-driven digital maturity. This frees up everyone’s focus on an improved production age in the future.